
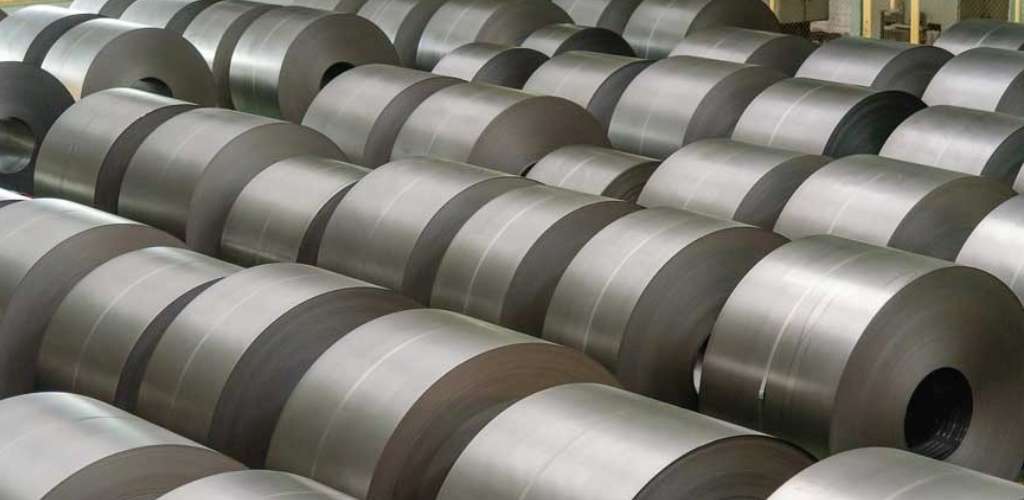
Hot Rolled vs Cold Rolled Steel: Understanding the Differences
Steel is one of the most versatile and widely used materials in the world, finding applications in everything from construction and manufacturing to automotive and aerospace industries. When it comes to rolling steel, two primary methods are used: hot rolling and cold rolling. These processes impart distinct characteristics to the steel, making it crucial to understand the differences between hot rolled steel and cold rolled steel. In this blog post, we'll delve into the technicalities of these processes and explore the unique properties each imparts to the steel.
Hot Rolled Steel
The Hot Rolling Process
Hot rolling manufacturing process involves rolling above the recrystallization temperature of steel, typically around 1700°F (926°C).
Hot rolled steels has a rough, scaly surface due to the oxidation that occurs at high temperatures. The scales are further removed by Pickling, Grinding & Shot Blasting. Hot rolled steels common applications include:
- Structural components in buildings and bridges
- Railroad tracks
- Pipes and tubes
- Agriculture equipment
AM/NS Hot rolled Steel (Attributes & Application)
- Best in Class Tolerances
- Guaranteed Flatness
- Consistency of Properties
- Customized & Wide Range of Sizes
Cold Rolled Steel
The Cold Rolling Process
Cold rolling is a process that involves rolling steel at ambient temperature. This process is performed after hot rolling, where the hot rolled steel is further processed to achieve
Hot Rolling | Cold Rolling |
---|---|
Steel Slab is fed to the rolls after being heated above the recrystallization temperature. | Hot Rolled Pickled coils are fed to the rolls when it is below the recrystallization temperature. |
In general, rolled steel does not shows work hardening effect. | The metal shows the working hardening effect after being cold rolled. |
Heavy reduction in area of the work piece can be obtained. | Heavy reduction is not possible. |
Surface finish parameter is not expected for HR product applications | Surface finish is excellent for aesthetic for CR product applications |
specific properties and dimensions. Cold rolling reduces the thickness of the steel and improves its surface finish.
Cold rolled steel offers both superior dimensional accuracy, with tight tolerances & a smooth, polished surface with a matte or satin-like appearance. This surface finish is ideal for applications that require a visually appealing and consistent look.
AM/NS Cold Rolled Steel (Attributes & Application)
In Summary:
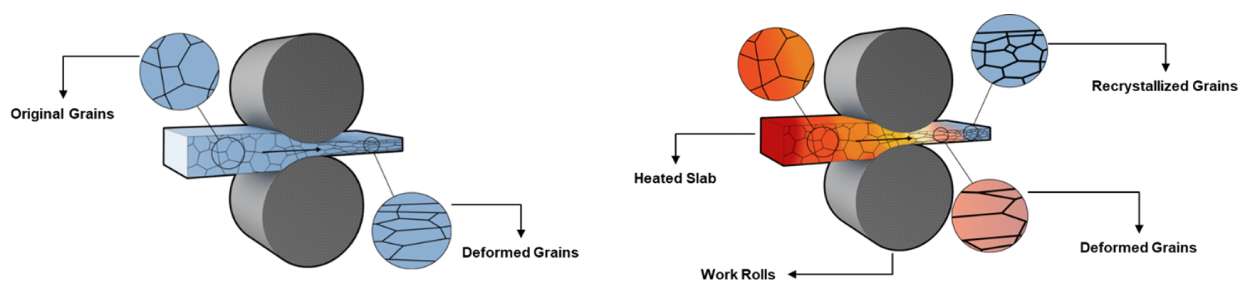
Choosing the Right Steel for Your Project
Selecting between hot rolled and cold rolled steel depends on the specific requirements of your project. Here are some factors to consider:
- End Application
- Operational Environment
- Strength & Durability
- Process Criticalities → Welding / Forming / Shearing / Surface Treatment
- Appearance & Surface Finish
Final take:
Understanding the differences between hot rolled steel and cold rolled steel is essential for making informed decisions in various applications. Each type of steel has its unique properties and advantages, making them suitable for specific use cases. Whether you prioritize cost-efficiency, strength, precision, or aesthetics, the choice between hot rolled and cold rolled steel ultimately depends on the particular requirements of your project. By considering these factors, you can ensure that you select the right steel product to meet your needs and achieve the desired results.

Explore our latest Post
- Market Dynamics: Analyzing The Demand And Supply Of Hot Rolled Steel In India
- Hot Rolled Steel Sheets And Coils: Versatile Industrial Materials
- The Role Of AM/NS Stallion In Improving Modern-Day Agriculture
- The Manufacturing Process Behind Hot Rolled Steel
- Hot Rolled vs Cold Rolled Steel: Understanding the Differences
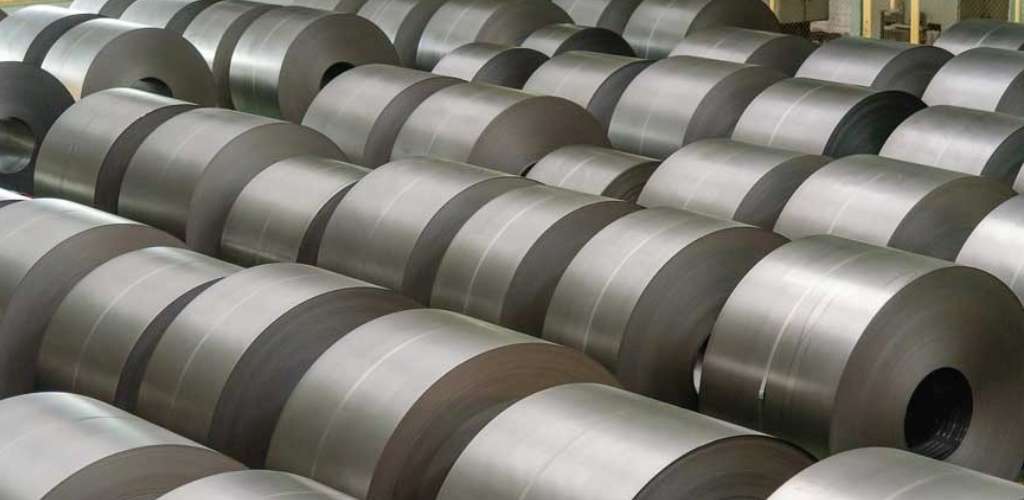